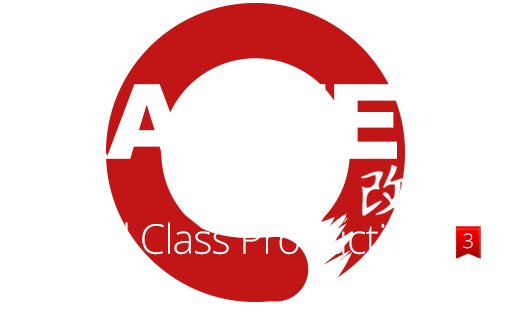
Vizuelizacija procesa
Kai-Zen
Organizacija radnog mesta
Pošto prvo sinhronizujemo tok procesa, a problemi u prodaji, nabavci, logistici, projektovanju i planiranju se više ne odražavaju u toj meri u procesu proizvodnje, spremni smo da ”siđemo dole”. Mikro organizacija ima smisla tek kada se otklone glavni uzročnici ,,Rasipanja“ , u fazama 1 i 2, Transformers i Just in Time. Mi to zovemo fino podešavanje procesa , jer sada razmišljamo o svakom detalju, pokretu i položaju. 5S, SMED, ErgoSAM i MTM su komplementarni alati koje istovremeno koristimo za dostizanje Kai-Zen organizacije radnog mesta.
5S
Lean alati su dokazali svoju primenljivost u industriji i svoju slavu su stekli upravo prednostima koje pruža njihova primena. Prednosti primene 5S alata mogu da se opišu sledećom rečenicom: 5S predstavlja metod za kreiranje organizovanog radnog mesta na način takav da se eliminišu rasipanja i nekorisne aktivnosti, ali i da se nepravilnosti koje se u svakodnevnom radu javljaju sa lakoćom uočavaju i eliminišu. Dakle, cilj primene ovog alata nije samo postizanje bolje organizacije jednokratnom akcijom, već stvaranje takvih uslova, da se novostvorena organizacija održava i poboljšava u kontinuitetu.
Kao što i sam naziv alata govori, ova metoda sadrži pet grupa pravila tj. koraka koje je potrebno izvršiti prilikom sprovođenja na radno mesto. U nastavku će biti opisan svaki od pet koraka.
Kao što je to slučaj prilikom uvođenja bilo kog standarda / pravila / procedure, tako je i prilikom uvođenja 5S-a potrebno obučiti tim ljudi koji će učestvovati u sprovođenju prvog projekta. Obuka podrazumeva upoznavanje članova tima sa osnovama Kaizen-a i Lean-a kroz praktične vežbe i primere prethodno sprovedenih 5S projekata u različitim industrijama.
Svrha ove obuke je, između ostalog, izgradnja očekivanja kod učesnika da je promena moguća i poželjna.
1S – Sortiraj
Cilj prvog koraka jeste da se stvari na određenom radnom mestu, u određenom prostoru sortiraju, tj. da se odvoji nepotrebno od potrebnog.
2S – Složi
Nakon što je u prethodnom koraku radno mesto rasterećeno nepotrebnih stvari, u drugom koraku preostale potrebne stvari se organizuju na način koji odgovara aktivnostima koje se obavljaju na datom radnom mestu.
Ovo podrazumeva detaljnije razmatranje načina rada, zbog čega je u ovom koraku poželjno mapirati aktivnosti na radnom mestu. Cilj ovog koraka jeste ustanoviti šta je od materijala / opreme potrebno prilikom izvršenja evidentiranih aktivnosti. Na taj način se ustanovljava potreba za nabavkom dodatne opreme, ali isto tako se često dešava da se ustanovi da se na radnom mestu nalazi još nepotrebnih stvari ili stvari u količinama većim od potrebne.
3S – Spremi
Tokom prethodna dva koraka radno mesto je oslobođeno nepotrebnih stvari, a stvari koje su potrebne su organizovane na način koji podržava tok procesa i ergonomiju rada.
Cilj trećeg koraka jeste da radno mesto bude čisto, s tim da je fokus na otklanjanju uzroka i na prevenciji, a ne samo na jednokratnom čišćenju radnog mesta. Često se sreće pogrešno tumačenje ovog koraka u tom smislu, što dovodi do narušavanja svrhe ovog koraka, ali često i svrhe 5S-a kao metode u celini.
Kada je reč o sprovođenju ovog koraka u kompaniji, važno je naglasiti važnost otkrivanja uzroka nastanka nečistoća koje se uklanjaju tokom akcije čišćenja. Na taj način, otkriven uzrok će biti osnova za osmišljavanje rešenja za eliminaciju istog. Tokom ovog koraka, fokus se takođe usmerava i na bezbednost radnog mesta.
4S – Standardizuj
Sprovođenjem prethodna tri koraka radno mesto je dovedeno u stanje u kakvom želimo da se nalazi svakodnevno. Upravo to jeste i cilj četvrtog koraka – obezbediti uslove i ustanoviti pravila (standarde) koji će podržati održivost rezultata koji su postignuti u prethodna tri koraka.
Faza standardizacije podrazumeva vizuelizaciju radnog mesta, izradu čeklisti, rasporeda, uputstava itd. Svrha vizuelizacije jeste da podrži i učini vidljivim pravila koja su postavljena u prethodnim koracima. U tom smislu, dobra vizuelizacija radnog mesta stvara uslove takve da se lako uočava da li postoje nepotrebne stvari na radnom mestu (1S-sortiraj), da li su stvari vraćene na svoje mesto (2S-složi) i da li su preuzeti koraci u održavanju čistoće prostora putem čeklisti (3S-spremi).
Vizuelizacija radnog mesta i prostora podrazumeva označavanje podova (transportni putevi, pozicije materijala, opreme), označavanje stolova, polica i tabli za alat (pozicije elemenata rada, indikatori količina, adrese), postavljanje oznaka koje se odnose na pravila i bezbednost itd. Prilikom vizuelizacije je važno ustanoviti standarde po pitanju upotrebe boja i vrsta označavanja, kako bi se obezbedila standardna upotreba na nivou svih radnih mesta. Takođe, poželjno je napraviti katalog za vizuelizaciju, kao dokument koji podržava prethodno sprovedenu standardizaciju.
5S – Samodisciplina
Sprovođenje petog koraka predstavlja najzahtevniju fazu. Postoji više razloga za ovo:
- Samodisciplina je nešto što se stiče dugotrajnim ponavljanjem i najčešće podrazumeva promenu navika. Mehanizam stvaranja navike je kompleksan i isti je izučavan na polju psihologije. Iako to možda deluje previše apstraktno u okvirima preduzeća, mehanizam stvaranja i promene navike je istovetan kako kod „ličnih“ navika, tako i kod radnih navika, koje se ispoljavaju u preduzeću, na radnim mestima.
- Konflikt kratkoročno-dugoročno. Iako nam razum govori da je rad na 5S-u opravdan, poželjan i potreban, u okruženju u kom nisu definisane vrednosti, pravila i prioriteti – kratkoročno uvek „pobeđuje“ dugoročno.
- Nepostojanje (Kaizen) kulture. Da bi bilo koji standard, pa tako i 5S uistinu ostvario svoju svrhu, potreban je temelj koji počinje od kulture organizacije. To podrazumeva svakodnevno učešće i podrška svih zaposlenih. Najčešće izostaje adekvatno učešće i podrška rukovodstva, kako na tom nivou često postoji stav o tome da je 5S nešto što je previše operativnog karaktera da bi zahtevalo pažnju rukovodećih nivoa.
- Motivacija. Moglo bi se reći da nedostatak motivacije predstavlja jedan od uzroka za prethodno navedene probleme pri sprovođenju petog koraka.
Na osnovu prethodno navedenih prepreka, preporuke za sprovođenje petog koraka su sledeće:
- Naglašavanje važnosti
- Kreiranje i uvođenje audita
- Formiranje sistema nagrađivanja
- Davanje primera i promocija doslednosti
- 5S tabla praćenja Kaizen aktivnosti
- Prezentacije postignutih rezultata
- Uvođenje sistema predloga
Kao što je već rečeno, peti korak predstavlja najzahtevniju fazu uvođenja 5S-a. Ukoliko se ne istraje u naporima da se isti svakodnevno sprovodi, vremenom će skoro sva postignuća nestati i sve će se vratiti na prethodno zatečeno stanje.
Ako za trenutak zastanemo i ponovo vidimo, posmatramo ono ”što već znamo kako jeste” dešava se čudo kojem sam prisutvovao puno puta. Kao u onim lepim filmovima gde glavni glumac traga za zakopanim blagom na kraju filma shvata da to ”blago” za kojim je tragao je sve vreme bilo tu, ispred njega.
Čudo se nalazi u zajedničkoj promeni perspektive i uviđanju stvarnog potencijala unapređenja sopstvenih postojećih resursa bez kapitalnih ulaganja i naravno akciji koja je zbog zajedničkog fokusa dobila snagu koja se manifestuje kroz praktičnu implementaciju i zajedničku želju da se održe postignuti nivoi.
MDC-Method Design Concept
MDC (Method Design Concept) predstavlja tehniku koja omogućava analizu, kako manuelnih, tako i mehanizovanih procesa u proizvodnim i uslužnim delatnostima. Osnovno polazište MDC-a nalazi se u tome što se pri analizi postojećih metoda sve aktivnosti klasifikuju na bazne i pomoćne aktivnosti u zavisnosti od toga da li direktno doprinose obavljanju operacije.
Razlika između ove i tradicionalnih metoda se nalazi u pristupu analizi aktivnosti. Tradicionalnim metodama radimo i delujemo polazeći „spolja-ka-unutra“, poboljšavamo ono što imamo i eliminišemo ono što je nepotrebno. MDC podrazumeva ciljno usmeren „napad“ tj. „delovanje-iz-centra“, čime utvrđujemo minimum koji je potreban da bi se obezbedio tok procesa koji želimo da razvijamo, a zatim se ovo kompletira sa okolnim, neophodnim pomoćnim aktivnostima.
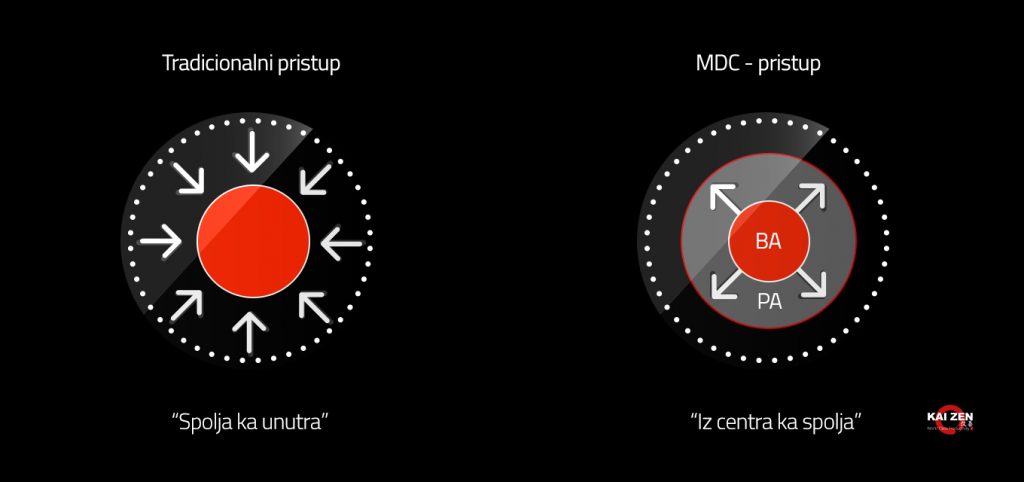
Bazne aktivnosti su one aktivnosti koje obezbeđuju svrhu procesa (pretvaranje inputa u outpute). Ovim aktivnostima dodajemo pomoćne aktivnosti koje su neophodne i koje, zajedno sa baznim aktivnostima, obezbeđuju željeni proces. Na ovaj način izgrađujemo najracionalniji metod za proces, polazeći iz centra ka spolja, prema cilju koji smo postavili u početku – povećanje produktivnosti.
Ukoliko posmatramo operatera koji je zadužen za dopunjavanje sirovina na liniji keksa ili službenika koji radi na otvaranju računa, onda možemo da kažemo da je njegova bazna aktivnost odvija upravo u trenutku dok sipa brašno u mikser ili dok unosi podatak. Sve ostale aktivnosti nazivamo pomoćnim aktivnostima i rasipanjima. Tako će, primera radi, provera nivoa, kontrola, odlazak u magacin po sirovine, čitanje podataka i pristupanje dokumentaciji kroz softver predstavljati pomoćne aktivnosti, a traženje po magacinu podataka i prepravljanje pogrešno upisanih podataka će predstavljati rasipanja.
Kako želimo da maksimalno iskoristimo ono što imamo na raspolaganju (bez kapitalnih investicija) – nećemo menjati baznu aktivnost. To znači da nećemo, npr. investirati u nabavku automatizovanog sistema koji bi zamenio operatera/službenika. Koristeći MDC pristup, definisaćemo da je ta bazna aktivnost operatera/službenika minimum od kojeg krećemo. Trajanje pomoćnih aktivnosti ćemo smanjiti tako što ćemo aktivnosti procesa i sama radna mesta organizovati na takav način da rasipanja budu eliminisana i pomoćne aktivnosti imaju manje učešće u odnosu na baznu aktivnost. Cilj je da proces, njegovi segmenti, pa i sama radna mesta budu organizovana na način takav da zaposleni veći deo radnog vremena provode u sprovođenju baznih aktivnosti.
MTM – Method Time Measurement & ErgoSAM
Sekvencama bazirana analiza aktivnosti
- Metod koji nudi unapred definisana vremena za sve potrebne aktivnosti/pokrete (sekvence) kako bi se za neki definisan posao/proceduru mogla utvrditi vremenska vrednost jednakog značenja.
- Pošto se posao/procedura opiše sabiranjem MTM sekvenci dobijamo realno vreme za ceo posao/proceduru.
Metod MTM pruža korisnicima i različitim specijaistima jedno zajedničko analitičko razmišljanje.
(MTM) je jedan elementarni vremenski sistem uz čiju se pomoć svaka manuelna operacija može podeliti u osnovne pokrete koji su neophodni da se izvrši dotična radna operacija. Svakom od ovih osnovnih pokreta dodeljena je određena vremenska vrednost, koja je ranije utvrđena.
Vremenska jedinica koja se upotrebljava u MTM-u je TMU, -“Time Measurement Unit”. Jedan TMU predstavlja jedan stohiljaditi deo sata ili 0.00001 h.
Šta se dobija primenom MTM-a?
- Znajući koliko je potrebno vreme i resursi za određeni posao možemo izračunati troškove po jedinici usluge/proizvoda i cenu
- Mogućnost nagrađivanja po učinku
- Pri promeni vrste usluge/asortimana brže dolazimo do novih normi jer u bazi već imamo izračunat veći broj potrebnih vremena
- Lako uvođenje novih operatora/službenika u posao jer imamo razrađene poslove/procedure (posao se ne prenosi s kolena na koleno)
- Demistifikacija poslova , mogućnost da preopterećeno osoblje/odelenje rasteretimo, a ne dovoljno opterećeno osoblje/odelenje dodatno zaposlimo
- Mogućnost upoređivanje poslova/odelenja bez obzira da li rade iste ili različite poslove
- Dobijanje norma vremena zaposlenih, ne zavisno od inteziteta rada što omogućava da vreme pretvaramo u novac
- Mogućnost planiranja/dimenzionsanja poslova (rokovi, potreban br.zaposlenih)
MTM sam imao priliku da koristim od 1987 godine, učeći ga od oca Milana Nonkovića tokom projekata u Crvenoj Zastavi, Prvoj Petoletci, Kluzu, Beku itd. U to vreme u Jugoslaviji je bila razvijena visoko serijska industrija i MTM kao metod je imao veliku primenu zbog preciznost koja je omogućavala da operateri povećaju svoju učinkovitost veoma često i preko 100%, bez povećanja inteziteta rada. Tokom 90-tih smo bili svedoci velikih promena u industriji koja je dovela da je danas glavni focus u promenama, kratkim serijama i rokovima, zbog kojih MTM je, po mom mišljenju , postao previše spor i komplikovan, a bila je potrebna i obuka u trajanju od mesec dana (trening + praksa). MTM je nasledio MDC – Method Design Concept. Shigeyasu Sakamoto i Klaus Helmrich su kreatori ove metode, a sa Klaus Helmrichom sam imao prilike da radim na velikom broju projekata. Vrednost MTM-a je velika jer nas fokusira da razmišljamo o vrsti pokreta, da li možemo da smanjimo dužinu ili broj pokreta, da li ergonomija pokreta omogućava duži rad, da li koristimo obe ruke, kakav nam je položaj tela i ruku, koliko je bezbedan posao koji obavljamo, statičnost/dinamika pokreta, prokrvljenost ruku, itd. Sve navedeno moramo da uzmemo u obzir kada koristimo MDC kao metod jer nas ne tera da tako detaljno analiziramo pokret po pokret, ali omogućava da za kratko vreme obučimo operatere i inženjere da promene pespektivu i uz malu pomoć dolazimo do izvanrednih unapređenja, ali za drastično kraće vreme. MTM kao metod se i dalje koristi u industijama gde postoji proizvodna linija, kao što je auto ili tekstilna industrija, ali isto tako i u uslužnim delatnostima, u visoko repetativnim poslovima, npr. kod poslova u šalter sali, unosa podataka u računar, programiranju, i sl. Za ostale industrije, gde je akcenat malim serijama, brzim izmenama i kratkim rokovima, MTM je podsetnik da kada kreiramo novu procedure, organizujemo radno mesto, radimo nalog koji ima više od npr.10 komada, isplati se da razmišljamo i o ergonomiji tela, dinamici pokreta i efikasnosti ruku jer sve to utiče mnogo više nego što nam se na prvi pogled može činiti.
5 WHY radna nedelja
5 Why se sprovodi u trajanju od 5 radnih dana za svako pojedinačno radno mesto:
1 dan: Analiza aktivnosti – identifikacija aktivnosti koje ne stvaraju vrednost za kompaniju (sprovodi Lean analitičar na odabranom radnom mestu)
2 dan: MDC mapiranje i identifikacija uzročnika problema od strane operatera (rade zajedno Lean analitičar i operater)
3 dan: Komunikacija i odnosi sa drugim radnim mestima (rade zajedno Lean analitičar i operater)
4 dan: 4S – Unapređenje efikasnosti radnog mesta (rade zajedno Lean analitičar i operater na odabranom radnom mestu)
5 dan: 5 Why raport
Po obavljenom ciklusu može se očekivati da će sva radna vidno podići nivo efikasnosti, kako po pitanju obavljanja poslova (veći broj komada, kraće vreme izrade, brža priprema, bolja ergonomija i motivacija operatera), po pitanju smanjenja troškova (smanjenje grešaka i škarta, smanjenje zastoja kroz bolje održavanje alata i mašina), tako i kroz bolju međusektorsku saradnju (smanjenje čekanja, ponavljanja, grešaka, gomilanja,…).
Korist za kompaniju:
- Obučen Kaizen tim može da samostalno sprovodi procesna unapređenja u kompaniji
- Omogučava se konstantan rad na u napređenju procesa i procedura
- Proširivanje i produbljivanje Kanban praćenja na ostale procese
- Unapređenje i standardizacija radnih mesta – 5S
- Kontinualna analiza, traženje rešenja i sprovođenje dobrih rešenja aktuelnih po
- Standrardizacija i praćenje sprovođenja dobrih rešenja
- Dubinsko sticanje znanja o svakom radnom mestu u kompaniji
- Unapređenje efikasnosti rada svakog radnog mesta uz aktivno učestvovanje operatera koji tokom tog procesa postaje aktivan saradnik u kontinualnom unapređenju
- Kompanija dobija „svog“ čoveka koji stiče poštovanje od strane operatera po pitanju unapređenje poslova na mikro nivou.
- Kaizen tim uspostavlja i unapređuje procesnu komunikaciju između sektora i radnih mesta
- Kaizen tim barata sa realnim činjenicama i podacima koji se kreiraju zajedno sa operaterom/zaposlenim, što čini osnov za početak unapređenja jer je sagledavanje objektivno i prihvaćeno od strane operatera/zaposlenog
- Kaizen tim sagledava stvari objektivno i nepristrasno jer ima za cilj da uspostavi stabilne procesne tokove i kontinualno prenoseći „širu sliku“ svojim kolegama uspostavljaju saradnju između sektora
- Spremnost za profesionalno uvođenje 5S-a, Kanbana i SMED-a